What Are the Benefits of Routine Maintenance for Pumps?
- Zack Woo
- Apr 12
- 12 min read

The benefits of routine maintenance for pumps include increased efficiency, extended lifespan, and reduced operational costs. Regular centrifugal pump maintenance helps to identify and address potential issues before they become major problems, ensuring the smooth operation of centrifugal pumps. By maintaining centrifugal pumps on a scheduled basis, downtime is minimized, and the overall performance of the system is optimized.
How to maintain water pump?
To maintain a water pump, it is essential to perform regular inspections, clean components to prevent blockages, and check for any signs of wear or damage. Ensuring that the pump is properly lubricated and that seals and gaskets are intact will help maintain efficiency and prevent leaks.
Additionally, monitoring the system's performance and addressing any irregularities promptly can extend the lifespan of the pump and reduce unexpected downtime.
How to maintain water pump in house?
To maintain water pump in house, it is essential to conduct regular inspections, cleaning, and addressing potential issues like leaks and unusual noises.
Begin by checking the proper alignment of the pump to avoid excessive wear on the pump parts and ensure efficient operation.
Inspect the bearing housing regularly for any signs of overheating or unusual vibration, as these could indicate potential issues.
Mechanical seals should also be examined and replaced if damaged to prevent leaks and maintain optimal performance.
Cleaning and inspecting all pump parts, including the impeller and casing, will help remove any debris or buildup that can hinder functionality.
Implementing these pump maintenance procedures on a routine basis enhances the longevity of the pump while keeping it in peak condition.
What are the types of pump maintenance?
The types of pump maintenance include a comprehensive checklist to ensure consistent performance and longevity of the system.
Regular maintenance should start with inspecting for oil leaks, as leaks can indicate potential damage or inefficiency within the pump.
Additionally, unusual noises should be checked during operation, as they might signal mechanical issues or wear that requires attention.
It is essential to keep the maintenance history recorded to track past repairs and anticipate future needs effectively.
A thorough maintenance checklist also includes cleaning components, checking seals and bearings, and ensuring the alignment of parts.
By adhering to a regular maintenance schedule, the performance of the pump can be optimized, while also avoiding unexpected downtime and costly repairs.
What are the 4 aspects when performing maintenance on your pumps?
When performing maintenance on your pumps, the 4 aspects are pro-active preventive maintenance, condition based predictive maintenance, time-based predictive maintenance and breakdown or run-to-failure maintenance.
These 4 aspects are crucial to ensuring optimal performance and longevity.
A comprehensive pump maintenance program includes detailed maintenance tasks that need to be executed regularly.
Creating a maintenance checklist is vital, as it outlines all necessary maintenance activities. Implementing a regular maintenance routine helps in detecting issues early, reducing downtime, and extending the equipment's life.
An effective maintenance plan not only enhances efficiency but also minimizes unexpected failures, demonstrating the importance of systematic pump maintenance.

1) Pro-Active Preventive Maintenance
Pro-active preventive maintenance for pumps is a crucial strategy in pump maintenance that emphasizes regular, scheduled inspections and servicing to prevent breakdowns before they occur.
This approach involves monitoring pump performance, checking for wear and tear, lubricating moving parts, and replacing worn-out components.
By adopting pro-active preventive maintenance, you can ensure the longevity of your pumps, minimize unexpected downtime, and optimize operational efficiency, ultimately saving time and reducing pump maintenance cost in the long run.
2) Condition Based/ Predictive Maintenance
Condition based/ predictive maintenance revolves around monitoring the condition of pump systems to predict and prevent potential failures before they occur.
This method utilizes various diagnostic tools and monitoring technologies, such as vibration analysis and thermal imaging, to assess the health of the equipment in real-time.
By identifying issues early on, pump repair and maintenance can be strategically scheduled, minimizing unexpected downtimes and extending the lifespan of the pumps.
This proactive approach not only ensures operational efficiency but also reduces long-term maintenance costs.
3) Time-Based/ Preventive Maintenance
Time-based/ preventive maintenance involves scheduling regular pump maintenance at set intervals, regardless of the pump's current operating condition.
This proactive approach is designed to prevent unexpected failures and extend the life of the equipment.
By adhering to a fixed schedule, issues such as wear and tear can be identified and addressed before they escalate into major problems.
Implementing routine time-based maintenance ensures that pumps operate efficiently and reliably, reducing downtime and maintenance costs over time.
4) Breakdown/ Run-to-Failure Maintenance
Breakdown or run-to-failure maintenance is a reactive approach to pump maintenance. This method involves operating pumps until a malfunction or failure occurs, at which point repairs or replacements are performed.
While it may seem cost-effective in the short term due to the lack of regular maintenance expenses, it can lead to unexpected downtime and potentially higher repair costs.
This strategy is often used for non-critical pumps where unplanned failures do not significantly impact operations.
However, relying solely on run-to-failure maintenance can be risky for essential systems, making it crucial to balance this approach with other proactive maintenance strategies.

What is the purpose of pump maintenance?
The purpose of pump maintenance is to ensure the pump operates efficiently and reliably by addressing potential issues before they lead to significant problems.
Regular pump maintenance Singapore includes tasks such as inspecting for oil leaks, checking for unusual noises, and replacing worn spare parts, which can prevent unexpected failures and reduce repair costs.
Additionally, adhering to a maintenance schedule helps minimize downtime and extends the overall lifespan of the equipment.
1) Pumps are running as efficient as possible
Maintaining your pumps regularly is crucial for ensuring they run as efficiently as possible. Effective pump maintenance helps in identifying and addressing potential issues early, preventing unexpected breakdowns and costly repairs.
Routine maintenance ensures that all components are running smoothly, minimizing wear and tear, and optimizing performance.
By consistently focusing on the upkeep of your pumps, you enhance their reliability and longevity, which leads to more efficient operations and sustained productivity.
2) Reduces pump failure and down time
Effective pump maintenance is crucial to minimizing pump failure and reducing downtime. By adhering to a comprehensive pump maintenance program, you ensure that all components are inspected regularly and any issues are addressed promptly.
Establishing a maintenance schedule that includes regular check-ups helps in identifying potential problems before they escalate.
Implementing self flush pumps can significantly reduce the risk of blockages and enhance the pump's reliability.
Collaborating with a reputable pump manufacturer can provide you with specialized maintenance guidelines and solutions tailored to your equipment.
Overall, a well-structured industrial pump maintenance strategy is key to maintaining peak operational efficiency and extending the lifespan of your pumps.
3) Reduces equipment costs by extending the life of the equipment
Reducing equipment costs can be effectively achieved by extending the life of your pumps through regular maintenance.
By adhering to a thorough maintenance schedule, you can minimize the need for costly repairs that often arise from neglected upkeep.
Implementing corrective maintenance practices allows you to address issues promptly before they escalate into major problems.
Routine pump maintenance ensures that components are operating efficiently, reducing wear and tear and ultimately extending the operational lifespan of the equipment.
This proactive approach helps in maintaining optimal performance while significantly cutting down on replacement expenses.
4) Ensures that your pumps are not being neglected
To ensure that your pumps are not being neglected, it's essential to establish a routine maintenance schedule that guarantees each pump operates at optimal efficiency.
Regular inspections and maintenance help in identifying issues early, which can significantly reduce operating costs.
Key steps include checking the shaft pump alignment to ensure components are running smoothly and assessing the pump's health through predictive maintenance techniques.
By integrating these practices, you can maintain the longevity of your equipment and avoid unexpected failures.

Implementing a water pump preventive maintenance checklist is essential to ensuring the longevity and efficiency of your pump systems.
It's important to follow the pump manufacturer's guidelines as part of your proactive maintenance strategy.
Maintenance procedures should include a thorough visual inspection of the pump for any oil leaks or to ensure coupling alignment is correct.
Your maintenance team should monitor the discharge pressure to detect any irregularities and adhere strictly to the regular maintenance schedule.
Additionally, it's crucial to have the right inspection tools at hand to effectively perform these checks.
Maintaining a detailed maintenance history recorded helps in tracking performance and identifying recurring issues.
By performing daily checks and keeping up with your pump maintenance checklist, you're ensuring that your pump systems operate smoothly and efficiently.
Daily Check
Visual Inspection: Look for any obvious signs of wear and tear, leaks, or damage to the pump and surrounding area. Ensure there are no unusual noises or vibrations emanating from the pump while it is operating.
Check Pump Components: Verify the condition of the pump's valves, seals, and gaskets. Ensure they are intact and functioning correctly without any leaks.
Motor Temperature: Monitor the temperature of the pump motor to ensure it is within the recommended safe operating range. Overheating can indicate problems with the motor or pump efficiency.
Lubrication Levels: Check the lubrication levels in the bearings and other moving parts. Appropriate lubrication is crucial for reducing friction and wear on the components.
Flow Rate: Measure the flow rate of the pump to ensure it is operating at its optimal capacity. Any deviations could indicate an issue with the pump or system.
Pressure Gauges: Inspect the pressure gauges to ensure they are providing accurate readings. Maintain the pressure at the levels specified by the manufacturer.
Electrical Connections: Examine all electrical connections for signs of wear, corrosion, or looseness. Ensure that all safety and control devices are functioning properly.
Noise and Vibration: Listen for unusual noises and feel for abnormal vibrations that might indicate mechanical issues or misalignment within the pump system.
Suction and Discharge Lines: Check the suction and discharge lines for blockages or leaks. Ensure they are clear and secured properly.
Record Keeping: Document all findings and maintenance activities in the logbook. Consistent record keeping of all the maintenance activities help track the pump's performance over time and identify recurring issues.
Monthly Check
Inspect for Oil Leaks: Carefully examine the pump and surrounding areas for any signs of oil leaks. Leaking oil can indicate worn seals or other issues that need to be addressed immediately to avoid further damage.
Check for Excessive Vibration: Monitor the pump for any unusual vibrations. Excessive vibration can point to imbalances, misalignments, or worn bearings, which can impact the pump's efficiency and lifespan.
Evaluate the Mechanical Seal: Examine the mechanical seal for wear and tear. A faulty mechanical seal can lead to leaks and decreased performance, so it's crucial to ensure it is in good condition.
Inspect Piping and Connections: Check all pipes and connections for leaks, corrosion, and wear. Properly maintained connections ensure the smooth operation of the pump.
Test Pump Performance: Assess the pump's overall performance by measuring flow rates, pressure levels, and efficiency. Any anomalies might indicate underlying issues that need attention.
Lubricate Moving Parts: Ensure all moving parts, including bearings and couplings, are adequately lubricated. Proper lubrication reduces friction and wear, extending the pump's operational life.
Check Electrical Components: Inspect the motor, wiring, and other electrical components for signs of damage or wear. Secure connections and proper insulation are crucial for safe and efficient operation.
Clean the Pump and Surrounding Area: Regular cleaning helps prevent dirt and debris build-up, which can obstruct performance and lead to mechanical issues.
Quarterly Check
Inspect Alignment and Balance: Ensure the motor and shaft pump alignment are correct to prevent undue wear and tear. Check the balance to maintain operational efficiency.
Check for Leaks: Examine all seals, gaskets, and joints for any signs of leakage which could indicate wear or damage.
Lubricate Bearings: Proper lubrication of bearings is essential to prevent friction and overheating. Refer to the manufacturer's guidelines for the correct type of lubricant.
Review Vibration Levels: Use a vibration analysis tool to detect any unusual vibrations which could signify potential mechanical issues.
Inspect Electrical Connections: Ensure all electrical connections are secure and corrosion-free to maintain optimal power supply and reduce the risk of electrical failure.
Examine Pump Housing and Impeller: Check for signs of erosion, corrosion, or damage to the pump housing and impeller. Replace any worn parts to maintain efficiency.
Test System Pressure: Monitor the system pressure to ensure it remains within the recommended range, indicating the pump is operating correctly.
Flush Pump System: Perform a system flush to remove any debris or contaminants that may have accumulated, maintaining the cleanliness of the pump internals.
Update Maintenance Records: Document all actions performed during the quarterly check, noting any issues and the steps taken to resolve them for future reference and trend analysis.
Annual Check
Shaft Seals Inspection: Examine the shaft seals for any signs of wear or leakage. Replace if necessary to prevent fluid loss and maintain proper pump function.
Coupling Alignment: Verify the alignment of the coupling between the pump and the motor. Misalignment can cause excessive wear and tear on components.
Mechanical Seals Check: Assess the condition of the mechanical seals for any damage or deterioration. These seals are critical for preventing leaks and maintaining system integrity.
Motor Bearings Inspection: Inspect the motor bearings for proper lubrication and any signs of wear. Replace or lubricate as needed to ensure smooth operation.
Unusual Noises Check: Listen for any unusual noises that may indicate a problem with the pump or its components. Uncommon sounds can be a sign of impending failure.
Pump Head Pressure Check: Measure the head pressure to ensure the pump is operating within its designated parameters. Deviations can indicate potential issues that need addressing.
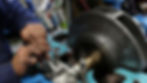
How often do I need a centrifugal pump maintenance?
You need a centrifugal pump maintenance every quarter of the year to ensure optimal performance and longevity.
During a centrifugal pump preventive maintenance, several critical tasks should be addressed. Conduct a head pressure check to confirm the centrifugal pump is operating within its specified range.
Ensure maintenance history is recorded meticulously to provide enough maintenance history for future reference.
Tighten bolts and inspect for oil leaks, which could indicate underlying issues. Proactively listen for unusual noises, as they can be an early indicator of problems to your centrifugal pumps.
Follow the pump manufacturer's guidelines closely to align with recommended maintenance practices.
This will not only improve your centrifugal pump performance but also reduce operating costs over time.
By diligently performing these maintenance tasks, you can enhance your centrifugal pumps' performance and extend their service life.
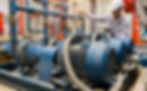
What is the importance of having maintenance on pumps?
The importance of having maintenance on pumps is paramount for ensuring seamless operation and optimal performance.
Regular maintenance ensures that critical components like the bearing housing and bearing reservoirs are in good condition, which is vital for the pump's health.
By taking proactive measures, you can detect and address unusual noises or other signs of distress before they escalate into significant issues.
This not only helps in preventing unexpected breakdowns but also reduces repair costs by catching problems such as pump cavitation early. What is pump cavitation and how do I avoid it?
Consistent maintenance helps the pump run smoothly, maintaining its efficiency and extending its lifespan.
Evaluating the pump's performance and health periodically allows for a more reliable and efficient pumping system, contributing to the overall effectiveness of your operations.
If maintenance does not resolve the issues, it may be necessary to replace the pump to ensure reliability and efficiency in your operations. Know when is it time to upgrade a water pump.
What is the advantage of routine maintenance?
The advantage of routine maintenance is that it ensures the pump operates efficiently and mitigates potential mechanical issues.
By implementing a consistent maintenance program, you can inspect impeller conditions, check axial float, and ensure proper alignment to keep the pump running smoothly.
Regularly checking for unusual noises can preemptively address problems, thereby preventing unexpected breakdowns.
Additionally, routine inspection of hydraulic governors and lubrication passages contributes to the overall health of the pump.
Keeping spare parts on hand also minimizes unexpected downtime, positively impacting the pump's performance. Recognize what are the symptoms and signs of a bad water pump and what are the common water pump problems and solutions.
In conclusion, committing to periodic maintenance enhances the longevity and reliability of the equipment while reducing both failure rates and operational costs.

What are the benefits of a maintenance plan?
The benefits of a maintenance plan include ensuring that your pump is running smoothly and efficiently.
By regularly checking aspects such as the pump's axial float, outer shell, and water cooling system, you prevent potential issues from escalating into costly repairs or unexpected downtime.
A well-maintained pump is crucial for optimal performance, maintaining kinetic energy transfer and ensuring consistent head pressure.
Proactive measures like routine head pressure checks, power source inspections, and unusual noises checks contribute significantly to the overall health and performance of your pumps.
Ultimately, a comprehensive maintenance plan extends the life of the equipment, reducing costs and enhancing reliability.
What is preventive maintenance for pumps?
For pumps, preventive maintenance is the inspection and repair scheduled at specific intervals (daily, weekly, monthly, yearly) or based on the number of hours run.
This proactive approach helps to avoid unexpected breakdowns and addresses mechanical issues before they escalate.
Key components such as pump parts, including the impeller, driver shaft, and seal chamber, should be routinely inspected. For a more detailed list, find out what are the key components of a water pump here.
Implementing a maintenance program that includes quarterly maintenance and timely checks for unusual noises ensures seamless operation.
By adhering to a preventive maintenance schedule, spare parts can be managed effectively, ensuring the pumps achieve optimal performance and longevity.
Routine maintenance is crucial for water pumps in industrial settings involves systematic inspections and servicing of components to ensure uninterrupted operation and prevent unscheduled downtime. Discover what are the different types of pumps in Singapore and where are water pumps commonly used in industrial settings.